sentric safety group’s talents
Meet Wajdi Ammar, Technical Manager, Sentric Tunisia
Wajdi has recently been promoted to Technical Manager, overseeing a team of four. Passionate about continuous improvement, he strives to value and encourage the work of each of his colleagues, making a point of creating an environment where collective excellence is recognised and celebrated.
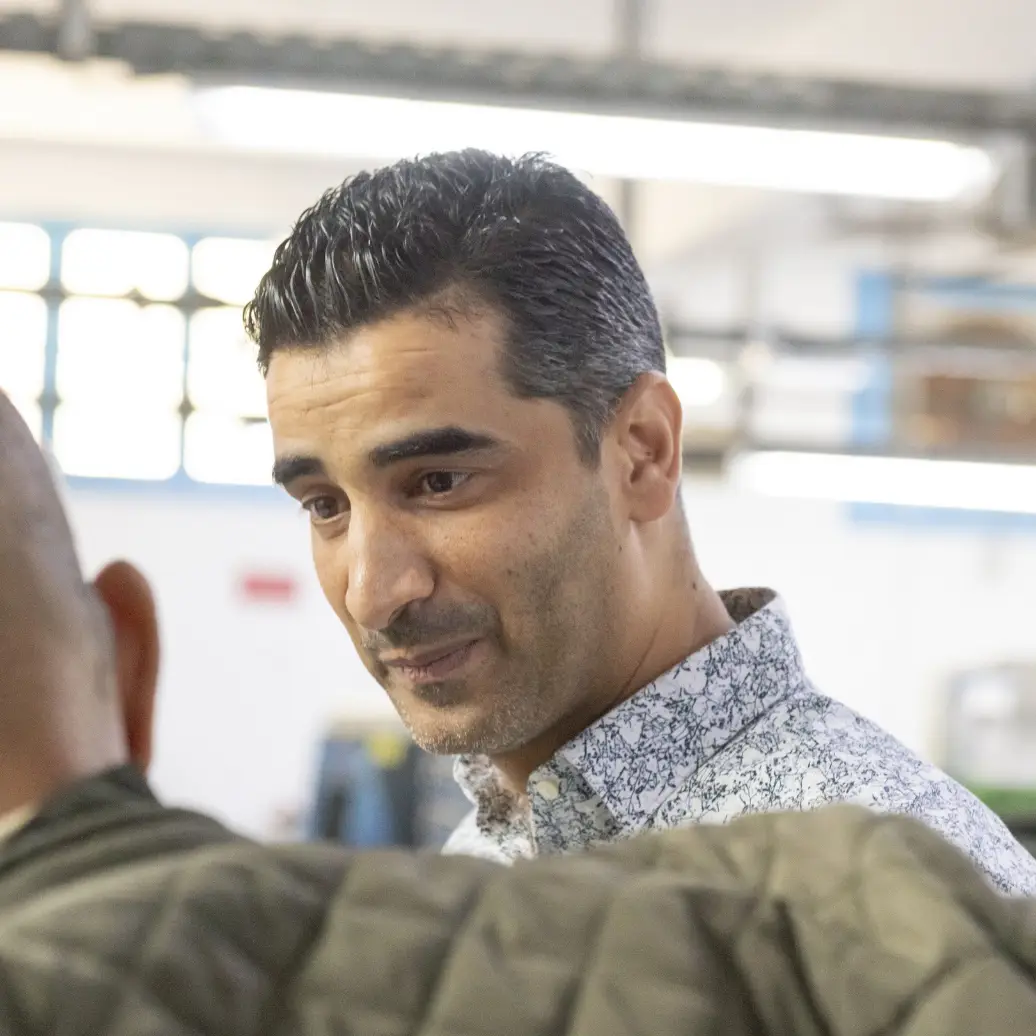
Tell us a little about yourself
My name is Wajdi Ammar. I grew up in Sfax, Tunisia, where I also did my higher education. I graduated from the École Nationale des Ingénieurs de Sfax with a degree in electromechanical engineering.
Before joining Sentric Tunisia, I had the opportunity to work for three different companies. I started my career in Zaghouan, in the automotive sector, and then returned to Sfax in 2011, during the revolution.
After that, I was attracted by international prospects and joined Leoni, a leader in energy and data management solutions for the automotive industry. Finally, I joined Sentric Tunisia in 2012 as a Methods Engineer.
What motivates you?
What motivates me is doing my job well and seeing opportunities for development within the group. I enjoy solving problems and contributing to the company’s development. Achieving our objectives is essential for me, because it has a positive impact on all employees. It affects everyone.
It’s important to me that my team and I devote part of our time to continuous improvement projects in Tunisia. These projects aim to facilitate the work of operators in the workshop and improve working conditions.
What do you like to do outside work?
Outside work, I’m a very devoted dad. I love coming home to spend time with my two-year-old daughter. We like to go for walks, take rides at the zoo or just enjoy the park. I also like to visit my family in my hometown.
What is your background at Sentric Tunisia?
I started at Sentric Tunisia in 2012 as a Methods Engineer. I’ve had the opportunity to work in various departments to provide technical support, which has enabled me to diversify my skills. In particular, I helped to improve the productivity and machining quality of our products in Tunisia.
I’m part of a project to optimise the plant’s workflows, including managing orders for new machines with our local suppliers. Since the beginning of 2024, I’ve built up my own team and now have four employees to better meet the requirements of current and future projects.
One of my team’s main objectives is the continuous improvement of production processes, including the installation of new machines and the optimisation of production lines to increase efficiency and reduce human error. For example, we recently introduced the use of QR codes to improve traceability and precision in product assembly.
What does a typical day look like for you?
My day usually starts with reading and answering urgent emails. Twice a week, we have team meetings to review the progress of projects and ongoing tasks. An important part of my job is to provide technical support to production. I can be called on at any time to clarify the use of a machine, provide drawings or give support to my team. When projects allow, I spend the quieter moments working on designs and plans.
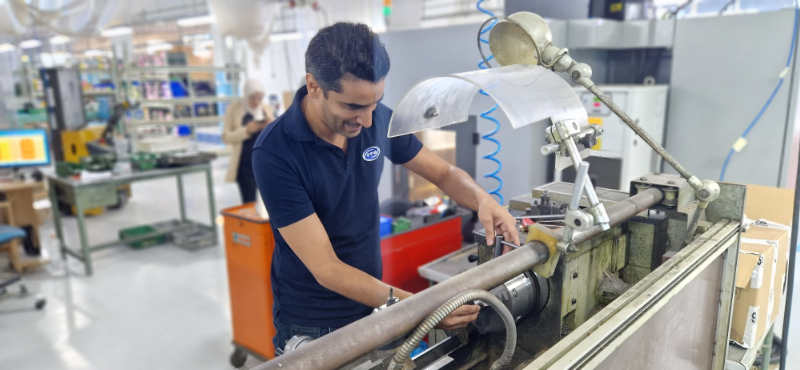
What do you like best about your job and the company?
What I like most is the working atmosphere. At Sentric Tunisia, it really feels like a family, with a positive and respectful atmosphere. I also enjoy working closely with my colleagues in Montreuil (STI) and learning from them. This allows me to train internally on specific databases and on the manufacture of our products.
What’s the most rewarding project you’ve worked on?
I’ve been involved in a number of projects, but two in particular are very close to my heart. I enjoyed working with our sales teams in France to develop a product for a major wind energy customer. This cooperation was crucial in meeting the customer’s expectations.
Another project I’m proud of was improving the working conditions of my colleagues by developing a system of semi-automatic pneumatic presses as well as two testing benches to facilitate pinning and quality control at the end of the line while ensuring the ergonomics and safety of the working stations.
Are there any areas in which you would like to improve?
Having recently moved into a managerial position, I’m keen to develop my management skills further. I actively participate in training courses to hone my skills in team management, communication and problem solving.
My aim is to create a collaborative and stimulating working environment, where each member of the team can flourish and contribute effectively to the company’s objectives. In the future, I plan to pursue standardisation and harmonisation initiatives, while exploring new technologies to continue optimising the performance of the team and the company.