As the holiday season approaches, the logistics and supply chain industry faces unique challenges and heightened demands. With increased consumer spending, seasonal product launches, and amplified shipping volumes, companies must address both logistical hurdles and safety concerns.
What are the critical effects of the holiday season on logistics and supply chain safety? We delve into these effects, with an emphasis on operational impacts and safety risks, and also look at best practices for managing them.
Increased volume and demand
Impact on logistics:
The holiday season triggers a surge in demand across multiple sectors, especially in retail, e-commerce, and transportation. As such, holiday shopping accounts for a significant percentage of annual sales for many businesses. As consumers place orders in larger quantities and with higher frequency, warehouses, distribution centres, and transportation networks must operate at full capacity.
Managing inventory becomes more complex as higher volumes require quicker restocking, precise demand forecasting, and careful oversight of stock levels to prevent shortages or excesses. Additionally, meeting holiday delivery timelines intensifies shipping and delivery pressures, compelling companies to handle complex schedules, increase shipping frequencies, and work with shorter lead times. This surge in activity also strains the workforce, often requiring temporary seasonal hires, which can introduce variability in skill levels and familiarity with company protocol.
Associated safety risks:
As operations scale up, safety concerns become increasingly prominent. Overcrowded warehouses and hurried employees heighten the risk of workplace accidents, especially when safety protocols are bypassed to save time. Extended working hours and high demands also contribute to employee fatigue and burnout, raising the likelihood of errors and accidents. The influx of new, seasonal workers further complicates safety; lacking familiarity with protocols, these inexperienced employees may inadvertently increase the risk of incidents due to limited training and experience.
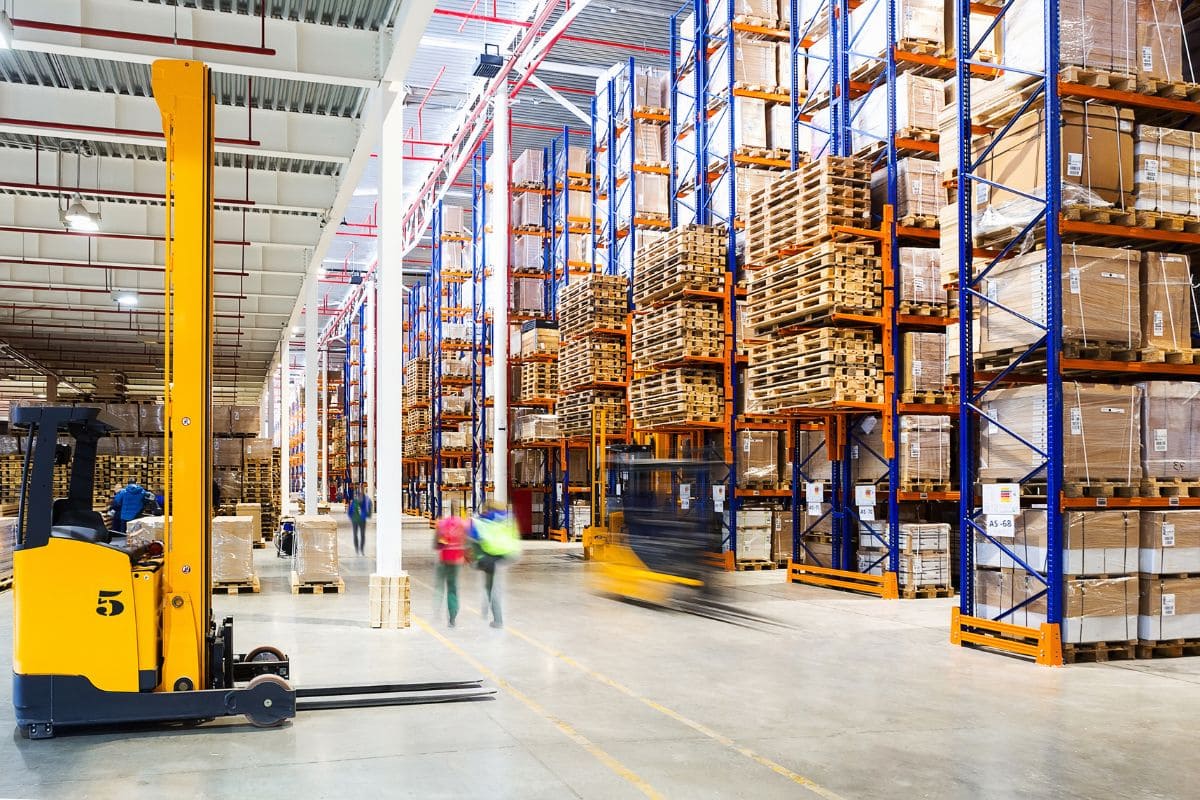
Complexities in transportation and last-mile delivery
Impact on logistics:
Holiday demand places significant strain on transportation networks, particularly in last-mile delivery, as companies work to meet tight deadlines amid high volumes. Capacity shortages often lead to transportation bottlenecks, with many carriers operating at or near maximum capacity. This high demand also drives up transportation costs, forcing companies to strategise carefully to balance cost control with efficiency.
Associated safety risks:
Drivers face considerable fatigue and pressure during peak delivery periods, with extended hours and tight schedules that increase the risk of accidents. Some companies may overextend transport capacity by overloading vehicles, leading to improperly balanced loads that elevate the risk of accidents and potential cargo damage.
Cybersecurity risks and digital safety concerns
Impact on logistics:
As more logistics operations integrate digital platforms and e-commerce plays a central role, cybersecurity becomes a pressing concern. Hackers often see the holiday season as an opportune time to target companies, hoping to exploit the urgency and higher transaction volumes. It’s hardly a surprise then that during peak seasons, companies face more cyber threats, including a higher risk of data breaches and ransomware attacks that can disrupt operations and compromise sensitive customer information.
The holiday season also underscores the business’ dependency on digital platforms; inventory management software, automated tracking systems, and e-commerce platforms become critical, leaving companies vulnerable if these systems are compromised. Scalability issues can also arise as handling high transaction volumes demands robust IT infrastructure, and strained systems may fail under heavy usage, potentially resulting in costly system collapses.
Associated safety risks:
Cybersecurity incidents can have direct impacts on physical safety within logistics operations. A cyberattack disrupting warehouse management systems can halt operations, potentially resulting in overloading or improper handling of materials. Compromised data security further exposes sensitive information, eroding customer trust and creating potential regulatory issues. Additionally, system outages may lead to communication breakdowns, preventing employees from accessing essential safety data or alerts, which elevates physical risks in logistics facilities.
Supply chain coordination and communication
Impact on logistics:
Meeting holiday demand requires seamless coordination across the entire supply chain, from suppliers and warehouses to end customers. However, the urgency of the season can strain communication channels, especially when multiple suppliers, transport providers, and internal departments are involved.
Supplier delays often trigger cascading disruptions throughout the supply chain, complicating efforts to keep operations on schedule. More holiday sales also lead to more returns, making efficient management of reverse logistics critical. To ensure cohesive operation, end-to-end visibility through real-time tracking and monitoring becomes essential, helping all parts of the chain to function in alignment.
Associated safety risks:
Poor communication within the supply chain can create hazardous situations, as misinformation and misalignment among stakeholders may lead to improper handling of materials or lapses in safety protocol adherence. Inventory mismanagement due to incorrect records or delays can result in stockouts or overstocking, heightening the risk of accidents in crowded storage areas. What’s more, inadequate coordination can slow emergency responses, particularly when partners are not aligned on safety protocols or response strategies, ultimately compromising overall workplace safety.
Best practices for enhancing logistics and supply chain safety during the holiday season
To effectively navigate holiday season pressures, logistics and supply chain professionals can implement several best practices that help mitigate risk:
Employee safety protocol training: Regular safety training sessions for both permanent and seasonal employees can reduce risks associated with inexperience.
Safety system implementation: Implementing a safety system in the warehouse or distribution centre that will safeguard against incidents like accidental drive aways will certainly reduce risk on site when the time and pressure of the holiday season is at an all-time high.
Workforce management and fatigue reduction: Scheduling shifts that allow employees adequate rest, providing additional resources, and monitoring employee wellness can reduce fatigue-related accidents.
Cybersecurity measures: Bolstering cybersecurity protocols, conducting regular system backups, and ensuring strong network defences can protect against cyber threats during this vulnerable period.
Enhance supplier and partner coordination: Establishing regular communication channels and ensuring clear alignment on timelines, capacity, and emergency protocols will help mitigate miscommunication-related risks.
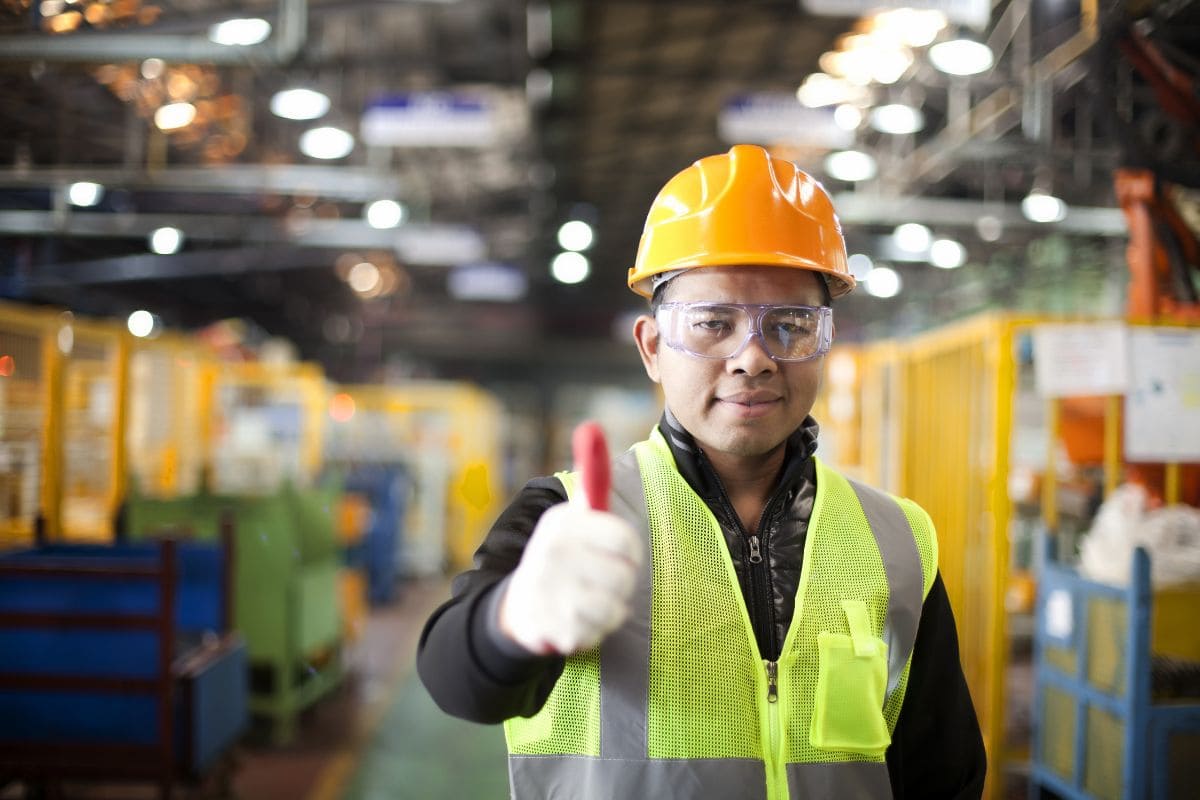
Impact made manageable
The holiday season brings both opportunity and risk for logistics and supply chain operations. By understanding the pressures and potential safety concerns, companies can implement strategies to mitigate risks, protect their workforce, and fulfil customer demands effectively. By focusing on enhanced training and robust safety protocol and system implementation, logistics companies can navigate the peak season efficiently while prioritising safety.
If your business operates in harsh, safety-critical environments, and you’re looking for safety solutions to safeguard your people, productivity and reputation during the holiday season, then the Sentric Safety Group, and Salvo, can help you. We have safety systems which can help you manage the pressures of peak season and protect your people and equipment on site at the loading bay.
For more information about what we do and how we can help you mitigate risk at busy times of the year, read more here: Loading Bay Solutions – Sentric Safety Group Global