News Archive
- Case Studies
- Company News
- Energy
- Industrial Manufacturing
- Insights
- People
- Rail
- Salvo Loading Safety
- Transport
- Warehouses
- Wind Power
- Zonegreen
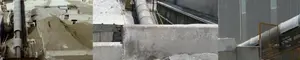
Precast Concrete Industry – Application Series: 1 of 5 Gravel Pits: Conveyor Systems
Gravel Pits: Conveyor Systems – Trapped …
Gravel Pits: Conveyor Systems – Trapped Key Interlock Safety Solutions. An estimated 18-20 per cent of all recorded health and safety incidents in quarry operations…
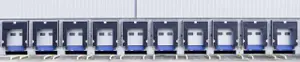
Minimizing the Loss of Energy at the Loading Dock
Loading docks are essential for facilities movement of goods. It is what allows their goods to reach their customers, ultimately creating revenue for the company. While loading docks are critical to enabling profits, they can also incur high energy costs.
The High Cost of Energy Loss
Inefficient energy usage can occur within a warehouse facility in a variety of ways, but the loading dock provides a large opportunity for generated energy to become wasted and for money to literally be thrown out the door. Warehouse facilities typically have numerous loading dock doors that are in use several hours a day, if not 24/7. Every second the dock door is open energy generated to produce the cool air or heat within the facility slips through the cracks. This issue is especially present in cold storage warehouses where a significant amount of energy is used to keep the facility cool and preserve the quality of the goods. An article from Star Refrigeration explains this further: “For a chilled facility at +2°C on a warm, humid day, where the ambient air is +32°C and 70% RH, air entering the building and being cooled to the +2°C condition requires around 100kJ/m3 of heat extraction. This corresponds to 100kW of energy per 1m3 of air entering the store. Assuming it is an efficient cooling system with a CoP of 3, this means 33kW of electrical energy is required to remove this heat – and at 6p/kWhr, this equates to a running cost of over £48 per day.” That cost can accumulate quickly coming in at £17,520 annually. In addition, the article goes on to say that if the goods were required to stay at a freezing temperature, such as -25C, the load and operating costs would increase by an additional 40%.Sustainability Solutions
Solutions are available to prevent the loss of energy through loading dock doors and the high costs associated with it. Loading dock seals and shelters are both relatively simple solutions that aid in temperature is control and minimize the amount of cool air or heat lost through the cracks of the trailer and dock. Seals are typically made from a foam material that compress when a trailer backs up to the dock during loading/unloading. This creates a suction like seal between the dockand trailer, limiting the cool air or heat escaping the warehouse. Loading dock shelters also limit the amount of cool air or heat escaping the warehouse and are typically used at sites where there are a variety of truck styles and sizes. They are not as effective as seals but still provide a sufficient solution to help reduce energy loss. In addition to seals and shelters, systems exist that only allow the dock door to be opened when a trailer is backed up to the dock and ready to be loaded/unloaded. For example, the Salvo Loading Dock Safety System ensures the dock door is locked closed until loading/unloading process can be performed safely. While a cool summer’s breeze may be enjoyable, precious energy and money are going to waste every second the dock door is left open. These systems greatly reduce the amount of energy going to waste at a facility and help companies save on energy costs. Sustainability is important and efficient energy usage is the first step to ensuring our environment is a clean and safe place for us to live and work for the foreseeable future. Make an impact at your facility today by implementing a solution to reduce the amount of energy lost at the loading dock.Loading docks are essential for facilities movement of goods. It is what allows their goods to reach their customers, ultimately creating revenue for the company. While loading docks are critical to enabling profits, they can also incur high energy costs.
The High Cost of Energy Loss
Inefficient energy usage can occur within a warehouse facility in a variety of ways, but the loading dock provides a large opportunity for generated energy to become wasted and for money to literally be thrown out the door. Warehouse facilities typically have numerous loading dock doors that are in use several hours a day, if not 24/7. Every second the dock door is open energy generated to produce the cool air or heat within the facility slips through the cracks. This issue is especially present in cold storage warehouses where a significant amount of energy is used to keep the facility cool and preserve the quality of the goods. An article from Star Refrigeration explains this further: “For a chilled facility at +2°C on a warm, humid day, where the ambient air is +32°C and 70% RH, air entering the building and being cooled to the +2°C condition requires around 100kJ/m3 of heat extraction. This corresponds to 100kW of energy per 1m3 of air entering the store. Assuming it is an efficient cooling system with a CoP of 3, this means 33kW of electrical energy is required to remove this heat – and at 6p/kWhr, this equates to a running cost of over £48 per day.” That cost can accumulate quickly coming in at £17,520 annually. In addition, the article goes on to say that if the goods were required to stay at a freezing temperature, such as -25C, the load and operating costs would increase by an additional 40%.Sustainability Solutions
Solutions are available to prevent the loss of energy through loading dock doors and the high costs associated with it. Loading dock seals and shelters are both relatively simple solutions that aid in temperature is control and minimize the amount of cool air or heat lost through the cracks of the trailer and dock. Seals are typically made from a foam material that compress when a trailer backs up to the dock during loading/unloading. This creates a suction like seal between the dockand trailer, limiting the cool air or heat escaping the warehouse. Loading dock shelters also limit the amount of cool air or heat escaping the warehouse and are typically used at sites where there are a variety of truck styles and sizes. They are not as effective as seals but still provide a sufficient solution to help reduce energy loss. In addition to seals and shelters, systems exist that only allow the dock door to be opened when a trailer is backed up to the dock and ready to be loaded/unloaded. For example, the Salvo Loading Dock Safety System ensures the dock door is locked closed until loading/unloading process can be performed safely. While a cool summer’s breeze may be enjoyable, precious energy and money are going to waste every second the dock door is left open. These systems greatly reduce the amount of energy going to waste at a facility and help companies save on energy costs. Sustainability is important and efficient energy usage is the first step to ensuring our environment is a clean and safe place for us to live and work for the foreseeable future. Make an impact at your facility today by implementing a solution to reduce the amount of energy lost at the loading dock.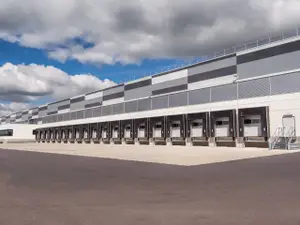
5 Tips to Select a Loading Dock Safety System for a New Warehouse Build
With e-commerce continuing to grow at increased rates, warehouse space is in high demand.
Retailers are looking to build new warehouses at a rapid rate and expand for distribution centres so that they can keep up with their growing inventory. According to the The Business Research Company’s Warehousing and Storage Global Market Report 2024, the warehousing and storage market size has grown strongly in recent years, from $724.47 billion globally in 2023 to $783.92 billion in 2024 (at a compound annual growth rate of 8.2%). What’s more, it’s expected that by 2028 it will have grown to $1062.19 billion (at a compound annual growth rate of 7.9%).
In addition to the demand for warehouse space, there is a demand for this space to be fitted with today’s latest technology and automation. This increase in technology and automation allows for retailers to maximize throughput and efficiency, however, it can also create a hazardous working environment where safety becomes secondary to speed of output.
Unfortunately, this type of environment often results in accidents, especially at the loading dock. 25% of all industrial accidents occur at the loading dock and 600 near misses occur for each accident. (OSHA)
To mitigate these risks, loading dock safety systems are commonly requested in new warehouse builds. Architects, engineers, specifiers, and owners are often responsible for selecting (or specifying) the loading dock safety system to incorporate into these projects.
With hundreds of loading dock safety products on the market, this decision can feel overwhelming. To help make the product specification simple, we have put together 5 tips to help you select a loading dock safety system for a new warehouse build:
1. Simple Installation Process
When searching for a loading dock safety product, select a product with a quick and simple installation process to minimize the risk of delays and downtime. Many systems on the market require complex concrete work to install vehicle restraints at the dock. However, there are products available that use other types of restraints, such as gladhands. Gladhand restraint systems lock out the vehicles air brakes, preventing movement and avoiding invasive concrete work installation.
2. Versatility
Warehouse design will differ from site to site and may use different loading structures, door types and vehicles depending on the facility’s location. Selecting a versatile solution that is compatible with a wide range of warehouse designs and vehicle types will save you time by allowing you to meet the requirements of multiple projects instead of only a single one.
3. Flexibility
Most loading dock safety products are permanent systems that cannot be removed from a warehouse facility once they have been installed. However, some loading dock safety systems offer the flexibility of a semi-permanent system. This can be an added benefit to a retailer who is building their own site but may want the flexibility to bring their loading dock safety system with them if they were to ever sell their warehouse and move locations in the future. With a semi-permanent system, a loading dock safety system is only purchased once – saving owners money if a facility’s location were to change in the future.
4. Lead Times
Selecting a product with a quick lead time will save time and avoid unnecessary delays. When considering a loading dock safety product to specify into a project, ensure lead times are reasonable and work with your project’s timeline. Lead time, installation time and your project timeline all need to be taken into consideration when selecting a loading dock safety system. Doing this ahead of time will avoid any surprises or delays in construction.
5. Customer Service
Great customer service is essential when looking for any product specified into a project design. Not only does the product you are looking to specify need to be of high quality but so do the people who you will be regularly interacting with and representing the product. It is important to select a product that is supported by a company and individuals who are considered to be experts. Working with a team whose focus isn’t only on sales but who truly want to help you solve an issue you are experiencing makes all the difference. Choose a product that has the support of honest, trustworthy, and service-oriented people behind it.
We hope these 5 tips help you select a loading dock safety system to specify for your next warehouse project.
If you have any questions, contact one of our Salvo loading dock safety experts today.
With e-commerce continuing to grow at increased rates, warehouse space is in high demand.
Retailers are looking to build new warehouses at a rapid rate and expand for distribution centres so that they can keep up with their growing inventory. According to the The Business Research Company’s Warehousing and Storage Global Market Report 2024, the warehousing and storage market size has grown strongly in recent years, from $724.47 billion globally in 2023 to $783.92 billion in 2024 (at a compound annual growth rate of 8.2%). What’s more, it’s expected that by 2028 it will have grown to $1062.19 billion (at a compound annual growth rate of 7.9%).
In addition to the demand for warehouse space, there is a demand for this space to be fitted with today’s latest technology and automation. This increase in technology and automation allows for retailers to maximize throughput and efficiency, however, it can also create a hazardous working environment where safety becomes secondary to speed of output.
Unfortunately, this type of environment often results in accidents, especially at the loading dock. 25% of all industrial accidents occur at the loading dock and 600 near misses occur for each accident. (OSHA)
To mitigate these risks, loading dock safety systems are commonly requested in new warehouse builds. Architects, engineers, specifiers, and owners are often responsible for selecting (or specifying) the loading dock safety system to incorporate into these projects.
With hundreds of loading dock safety products on the market, this decision can feel overwhelming. To help make the product specification simple, we have put together 5 tips to help you select a loading dock safety system for a new warehouse build:
1. Simple Installation Process
When searching for a loading dock safety product, select a product with a quick and simple installation process to minimize the risk of delays and downtime. Many systems on the market require complex concrete work to install vehicle restraints at the dock. However, there are products available that use other types of restraints, such as gladhands. Gladhand restraint systems lock out the vehicles air brakes, preventing movement and avoiding invasive concrete work installation.
2. Versatility
Warehouse design will differ from site to site and may use different loading structures, door types and vehicles depending on the facility’s location. Selecting a versatile solution that is compatible with a wide range of warehouse designs and vehicle types will save you time by allowing you to meet the requirements of multiple projects instead of only a single one.
3. Flexibility
Most loading dock safety products are permanent systems that cannot be removed from a warehouse facility once they have been installed. However, some loading dock safety systems offer the flexibility of a semi-permanent system. This can be an added benefit to a retailer who is building their own site but may want the flexibility to bring their loading dock safety system with them if they were to ever sell their warehouse and move locations in the future. With a semi-permanent system, a loading dock safety system is only purchased once – saving owners money if a facility’s location were to change in the future.
4. Lead Times
Selecting a product with a quick lead time will save time and avoid unnecessary delays. When considering a loading dock safety product to specify into a project, ensure lead times are reasonable and work with your project’s timeline. Lead time, installation time and your project timeline all need to be taken into consideration when selecting a loading dock safety system. Doing this ahead of time will avoid any surprises or delays in construction.
5. Customer Service
Great customer service is essential when looking for any product specified into a project design. Not only does the product you are looking to specify need to be of high quality but so do the people who you will be regularly interacting with and representing the product. It is important to select a product that is supported by a company and individuals who are considered to be experts. Working with a team whose focus isn’t only on sales but who truly want to help you solve an issue you are experiencing makes all the difference. Choose a product that has the support of honest, trustworthy, and service-oriented people behind it.
We hope these 5 tips help you select a loading dock safety system to specify for your next warehouse project.
If you have any questions, contact one of our Salvo loading dock safety experts today.