News Archive
- Case Studies
- Company News
- Energy
- Industrial Manufacturing
- Insights
- People
- Rail
- Salvo Loading Safety
- Transport
- Warehouses
- Wind Power
- Zonegreen
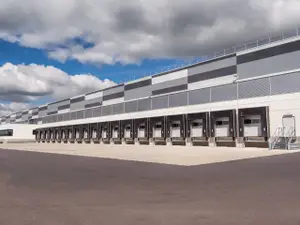
5 Tips to Select a Loading Dock Safety System for a New Warehouse Build
With e-commerce continuing to grow at increased rates, warehouse space is in high demand.
Retailers are looking to build new warehouses at a rapid rate and expand for distribution centres so that they can keep up with their growing inventory. According to the The Business Research Company’s Warehousing and Storage Global Market Report 2024, the warehousing and storage market size has grown strongly in recent years, from $724.47 billion globally in 2023 to $783.92 billion in 2024 (at a compound annual growth rate of 8.2%). What’s more, it’s expected that by 2028 it will have grown to $1062.19 billion (at a compound annual growth rate of 7.9%).
In addition to the demand for warehouse space, there is a demand for this space to be fitted with today’s latest technology and automation. This increase in technology and automation allows for retailers to maximize throughput and efficiency, however, it can also create a hazardous working environment where safety becomes secondary to speed of output.
Unfortunately, this type of environment often results in accidents, especially at the loading dock. 25% of all industrial accidents occur at the loading dock and 600 near misses occur for each accident. (OSHA)
To mitigate these risks, loading dock safety systems are commonly requested in new warehouse builds. Architects, engineers, specifiers, and owners are often responsible for selecting (or specifying) the loading dock safety system to incorporate into these projects.
With hundreds of loading dock safety products on the market, this decision can feel overwhelming. To help make the product specification simple, we have put together 5 tips to help you select a loading dock safety system for a new warehouse build:
1. Simple Installation Process
When searching for a loading dock safety product, select a product with a quick and simple installation process to minimize the risk of delays and downtime. Many systems on the market require complex concrete work to install vehicle restraints at the dock. However, there are products available that use other types of restraints, such as gladhands. Gladhand restraint systems lock out the vehicles air brakes, preventing movement and avoiding invasive concrete work installation.
2. Versatility
Warehouse design will differ from site to site and may use different loading structures, door types and vehicles depending on the facility’s location. Selecting a versatile solution that is compatible with a wide range of warehouse designs and vehicle types will save you time by allowing you to meet the requirements of multiple projects instead of only a single one.
3. Flexibility
Most loading dock safety products are permanent systems that cannot be removed from a warehouse facility once they have been installed. However, some loading dock safety systems offer the flexibility of a semi-permanent system. This can be an added benefit to a retailer who is building their own site but may want the flexibility to bring their loading dock safety system with them if they were to ever sell their warehouse and move locations in the future. With a semi-permanent system, a loading dock safety system is only purchased once – saving owners money if a facility’s location were to change in the future.
4. Lead Times
Selecting a product with a quick lead time will save time and avoid unnecessary delays. When considering a loading dock safety product to specify into a project, ensure lead times are reasonable and work with your project’s timeline. Lead time, installation time and your project timeline all need to be taken into consideration when selecting a loading dock safety system. Doing this ahead of time will avoid any surprises or delays in construction.
5. Customer Service
Great customer service is essential when looking for any product specified into a project design. Not only does the product you are looking to specify need to be of high quality but so do the people who you will be regularly interacting with and representing the product. It is important to select a product that is supported by a company and individuals who are considered to be experts. Working with a team whose focus isn’t only on sales but who truly want to help you solve an issue you are experiencing makes all the difference. Choose a product that has the support of honest, trustworthy, and service-oriented people behind it.
We hope these 5 tips help you select a loading dock safety system to specify for your next warehouse project.
If you have any questions, contact one of our Salvo loading dock safety experts today.
With e-commerce continuing to grow at increased rates, warehouse space is in high demand.
Retailers are looking to build new warehouses at a rapid rate and expand for distribution centres so that they can keep up with their growing inventory. According to the The Business Research Company’s Warehousing and Storage Global Market Report 2024, the warehousing and storage market size has grown strongly in recent years, from $724.47 billion globally in 2023 to $783.92 billion in 2024 (at a compound annual growth rate of 8.2%). What’s more, it’s expected that by 2028 it will have grown to $1062.19 billion (at a compound annual growth rate of 7.9%).
In addition to the demand for warehouse space, there is a demand for this space to be fitted with today’s latest technology and automation. This increase in technology and automation allows for retailers to maximize throughput and efficiency, however, it can also create a hazardous working environment where safety becomes secondary to speed of output.
Unfortunately, this type of environment often results in accidents, especially at the loading dock. 25% of all industrial accidents occur at the loading dock and 600 near misses occur for each accident. (OSHA)
To mitigate these risks, loading dock safety systems are commonly requested in new warehouse builds. Architects, engineers, specifiers, and owners are often responsible for selecting (or specifying) the loading dock safety system to incorporate into these projects.
With hundreds of loading dock safety products on the market, this decision can feel overwhelming. To help make the product specification simple, we have put together 5 tips to help you select a loading dock safety system for a new warehouse build:
1. Simple Installation Process
When searching for a loading dock safety product, select a product with a quick and simple installation process to minimize the risk of delays and downtime. Many systems on the market require complex concrete work to install vehicle restraints at the dock. However, there are products available that use other types of restraints, such as gladhands. Gladhand restraint systems lock out the vehicles air brakes, preventing movement and avoiding invasive concrete work installation.
2. Versatility
Warehouse design will differ from site to site and may use different loading structures, door types and vehicles depending on the facility’s location. Selecting a versatile solution that is compatible with a wide range of warehouse designs and vehicle types will save you time by allowing you to meet the requirements of multiple projects instead of only a single one.
3. Flexibility
Most loading dock safety products are permanent systems that cannot be removed from a warehouse facility once they have been installed. However, some loading dock safety systems offer the flexibility of a semi-permanent system. This can be an added benefit to a retailer who is building their own site but may want the flexibility to bring their loading dock safety system with them if they were to ever sell their warehouse and move locations in the future. With a semi-permanent system, a loading dock safety system is only purchased once – saving owners money if a facility’s location were to change in the future.
4. Lead Times
Selecting a product with a quick lead time will save time and avoid unnecessary delays. When considering a loading dock safety product to specify into a project, ensure lead times are reasonable and work with your project’s timeline. Lead time, installation time and your project timeline all need to be taken into consideration when selecting a loading dock safety system. Doing this ahead of time will avoid any surprises or delays in construction.
5. Customer Service
Great customer service is essential when looking for any product specified into a project design. Not only does the product you are looking to specify need to be of high quality but so do the people who you will be regularly interacting with and representing the product. It is important to select a product that is supported by a company and individuals who are considered to be experts. Working with a team whose focus isn’t only on sales but who truly want to help you solve an issue you are experiencing makes all the difference. Choose a product that has the support of honest, trustworthy, and service-oriented people behind it.
We hope these 5 tips help you select a loading dock safety system to specify for your next warehouse project.
If you have any questions, contact one of our Salvo loading dock safety experts today.
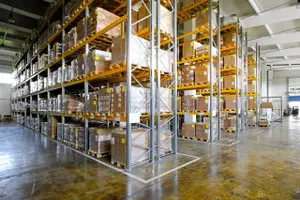
NSK improves loading bay safety at Netherlands warehouse
NSK, one of the world’s leading manufacturers of industrial and automotive components, has chosen Castell’s drive-away safeguard system Salvo™ to protect staff at its warehouse in Tilburg, Netherlands. NSK’s huge facility distributes more than 4,000 pallets a month across the whole of Europe and North Africa. Customers include Ford, Volkswagen, Siemens and Bosch. Salvo™ has been installed on 12 loading bays, while NSK has also bought four Salvo™ Club steering wheel locks to safeguard deliveries made by rigid vehicles. There have been no reported health and safety incidents since Salvo™ was commissioned at the Tilburg site. Having reversed their vehicle onto the relevant loading bay, drivers install the Salvo™ SGL lock on the exposed emergency airline coupling, releasing a trapped key. This key is then inserted and turned in the Salvo™ Control Panel (SCP+) on the outside of the bay. An amber beacon illuminates on the inside to indicate that the loading bay is now safe and ready to use. The loader opens the door, trapping the key in the SCP+ outside. While the door remains raised and the key trapped in the control panel, the trailer cannot be moved. NSK has also installed Salvo™ at its distribution centre in Newark, UK.
NSK, one of the world’s leading manufacturers of industrial and automotive components, has chosen Castell’s drive-away safeguard system Salvo™ to protect staff at its warehouse in Tilburg, Netherlands. NSK’s huge facility distributes more than 4,000 pallets a month across the whole of Europe and North Africa. Customers include Ford, Volkswagen, Siemens and Bosch. Salvo™ has been installed on 12 loading bays, while NSK has also bought four Salvo™ Club steering wheel locks to safeguard deliveries made by rigid vehicles. There have been no reported health and safety incidents since Salvo™ was commissioned at the Tilburg site. Having reversed their vehicle onto the relevant loading bay, drivers install the Salvo™ SGL lock on the exposed emergency airline coupling, releasing a trapped key. This key is then inserted and turned in the Salvo™ Control Panel (SCP+) on the outside of the bay. An amber beacon illuminates on the inside to indicate that the loading bay is now safe and ready to use. The loader opens the door, trapping the key in the SCP+ outside. While the door remains raised and the key trapped in the control panel, the trailer cannot be moved. NSK has also installed Salvo™ at its distribution centre in Newark, UK.
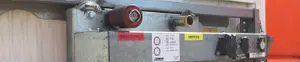
Fyffes chooses Salvoâ„¢ for UK distribution centres
Fyffes one of the leading importers …
Fyffes one of the leading importers and distributors of tropical produce has installed Castell’s Salvo™ drive-away safeguard system at its UK distribution centres
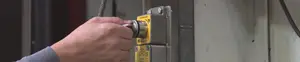
Bonmarché banishes drive-aways with Salvo™
Bonmarché, the UK’s largest value womenswear retailer for women aged 50+ years, has improved the safety of its loading and unloading operations with the adoption of Castell’s Salvo™. The interlocking drive-away prevention system has been installed on all seven loading bays at Bonmarché’s Grange Moor head office, near Wakefield, West Yorkshire. Grange Moor, Bonmarché’s only distribution centre, handles an average of 140,000 garments a day, although this rises to 200,000 at peak times. Third-party drivers arriving at Grange Moor report to security and receive documentation explaining how the Salvo™ system operates. They park in a holding area, where they are met by a supervisor who checks that they understand the information they have been given. Drivers are then asked to reverse into a particular loading bay, before disengaging their engine and fitting either a Salvo™ Susie or SGL lock to their vehicle’s exposed emergency airline coupling. This action effectively immobilises the trailer and releases a key, which the driver hands to a member of the warehouse staff. Inserting and turning the key in the control panel located next to the bay door powers up the bay and enables the door to be raised. Once the dock leveller has been correctly positioned, the driver is asked to pull the cab away, park in the holding area and wait there until further notice while unloading takes place. Goods-out follows a similar procedure, except that Bonmarché’s warehouse staff fit the Salvo™ Susie or Salvo™ Club, an interlocking steering wheel lock, to the vehicle prior to loading.
Bonmarché, the UK’s largest value womenswear retailer for women aged 50+ years, has improved the safety of its loading and unloading operations with the adoption of Castell’s Salvo™. The interlocking drive-away prevention system has been installed on all seven loading bays at Bonmarché’s Grange Moor head office, near Wakefield, West Yorkshire. Grange Moor, Bonmarché’s only distribution centre, handles an average of 140,000 garments a day, although this rises to 200,000 at peak times. Third-party drivers arriving at Grange Moor report to security and receive documentation explaining how the Salvo™ system operates. They park in a holding area, where they are met by a supervisor who checks that they understand the information they have been given. Drivers are then asked to reverse into a particular loading bay, before disengaging their engine and fitting either a Salvo™ Susie or SGL lock to their vehicle’s exposed emergency airline coupling. This action effectively immobilises the trailer and releases a key, which the driver hands to a member of the warehouse staff. Inserting and turning the key in the control panel located next to the bay door powers up the bay and enables the door to be raised. Once the dock leveller has been correctly positioned, the driver is asked to pull the cab away, park in the holding area and wait there until further notice while unloading takes place. Goods-out follows a similar procedure, except that Bonmarché’s warehouse staff fit the Salvo™ Susie or Salvo™ Club, an interlocking steering wheel lock, to the vehicle prior to loading.
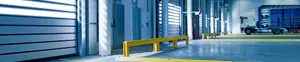
Dairy Crest improves loading bay safety with Salvo
Dairy Crest the UK’s leading chilled …
Dairy Crest the UK’s leading chilled dairy foods company is protecting loading bay personnel at two sites with Castell’s interlocking driveaway safeguard system Salvo